Produktionsprozesse sind durch Einflüsse aus den Bereichen Material, Technologie und Mitarbeiter fehleranfällig, wodurch Nacharbeit notwendig wird. Ziel ist daher, dies durch schnelles Erkennen und Beheben von Abweichungen während der Produktion zu umgehen. Hierzu wurde zusammen mit der Technischen Universität Darmstadt, MAN Truck & Bus, Magna Steyr und SFM Systems ein dreistufiger Ansatz zu folgender zentraler Fragestellung entwickelt:
Wie können Nacharbeits-Daten während der Produktion so verknüpft werden, dass gleichzeitig Kosten reduziert, Zeit gewonnen und außerdem die Mitarbeitenden bei ihrer täglichen Arbeit unterstützt werden?
Die Antwort: Die Neuartigkeit dieses Ansatzes liegt in der Verschmelzung von quantitativen (z.B. Maschinen- & Prozessdaten) und qualitativen Daten (Nacharbeitsdokumentation) durch die Adaption von Data-Analytics- und Machine-Learning Methoden
Vielversprechende Ergebnisse!
- Hohe Übereinstimmung der vorhergesagten Qualitätsprobleme während der Produktion
- 20%-ige Vorhersage sowie Erreichung einer erhöhten Awareness für weitere 25%
Aufbau des Ansatzes
Um diese Ziele zu erreichen wird ein dreistufiger Ansatz gewählt. Die Abbildung zeigt das Vorgehen in Zusammenhang mit Quality-Gates im Produktionsprozess (1).
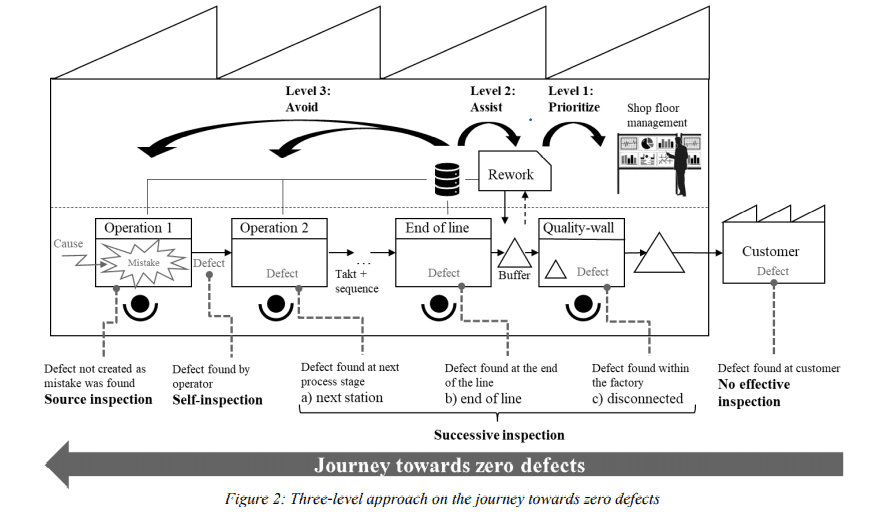
Stufe 1: priorisierung
Die Praxis hat gezeigt, dass Unternehmen oft nicht wissen, wo sie mit den Problem-lösungsaktivitäten während, oder nach der Produktion beginnen sollen. Der Ansatz sieht als ersten Schritt vor, die wichtigsten Fehler anhand von Gesamtzeitaufwand, Trend und Häufigkeit zu identifizieren.
Hierbei soll ein Fehler-Score helfen, dem Shopfloor-Team einen Überblick über Fehlercluster, sowie die Wahrscheinlichkeit jeden Fehlers zu geben und gleichzeitig als Entscheidungshilfe zu dienen, auf welche Probleme sich konzentriert werden soll (Priorisierung anhand der Merkmalsauswahl, z.B.: Produktfamilie, Datum des Fehlerauftretens, Fehlerort, Fehlerart und Nacharbeitsdauer).
Möchtest Du mehr über Führung in der Produktion erfahren?
Stufe 2: Assistenz
Durch maschinelles Lernen sollen dem Team konkrete Handlungsempfehlungen gegeben werden. Basierend auf der Priorisierung werden in der zweiten Ebene derzeit zwei unterschiedliche Assistenzfunktionen entwickelt:
- Verkürzung der Durchlaufzeiten bei der Nacharbeit (durch Handlungsempfehlungen bei der Fehlersuche, sowie der Lösung ergibt sich der Aufbau eines Wissensmanagement)
- Unterstützung der Kapazitätsplanung
Ziel: Vorhersage von Fehlerort und -art, sowie des notwendigen Zeitaufwands für die Nacharbeit auf Basis von Prozess- und Testdaten aus der Linie zusammen mit dem geplanten Produktionsprogramm.
Stufe 3: Vermeidung
Ziel: Vollständige Vermeidung von Nacharbeit durch Inline-Handlungsempfehlungen auf Basis von Daten aus vorangegangenen Prozessen:
Durch den Einsatz automatisierter Datenanalysen und maschinellem Lernen können mögliche Ursachen schneller identifiziert und über Handlungsempfehlungen behoben werden. Frühere Nacharbeitsaktivitäten können nun als gezielte Sofortmaßnahme durchgeführt werden. In der Summe führen sie zu einem umfassenden digitalisierten Shopfloor Management.
Zusammengefasst soll diese Stufe:
- sowohl die Selbst- als auch die Quellenprüfung unterstützen
- Um Nacharbeitsprobleme erst gar nicht entstehen zu lassen, benötigen die Mitarbeiter an der Linie eine Informationsunterstützung während des Arbeitsprozesses. Deshalb kombiniert die dritte Assistenzfunktion daher Daten über das Fertigungsprogramm mit kritischen Fehlern an Linienabschnitten
- Durch die Identifizierung potenzieller Fehler aus historischen Daten und die Zuordnung dieser Fehler zu Arbeitsstationen, können die Arbeiter auf diese kritischen Fehler aufmerksam gemacht werden.
Ausblick:
Eine Herausforderung in der industriellen Umgebungen ist die Qualität der analysierten Daten.
Daher werden in zukünftigen Projekten Mechanismen entwickelt, die die beschriebenen Fehler identifizieren und normalisieren, um die Datenbasis für die Datenanalyse zu vergrößern und mit den verwendeten Systemmodellen näher an die Realität heranzukommen.
(1) Longard; Brungs; Hertle; Röth; Metternich (2021): „Reduced rework through data analytics and machine learning – a three level development approach“, 11th Conference on Learning Factories CLF 2021, Graz, Austria, in print
Mehr über die Funktionen des Digital Teamboards erfahren
Folge uns
Verwandte Artikel
Was bedeutet Digital Shopfloor Management
In der heutigen Industrielandschaft, geprägt von stetigem Wandel und wachsendem Wettbewerb, stehen Produktionsunternehmen vor der Herausforderung, Effizienz zu maximieren und Kosten zu minimieren, ohne dabei Kompromisse bei der Qualität einzugehen. Die Antwort auf...
Schritte zur Implementierung einer digitalen Shopfloor Software in der Produktion und Fertigung
Digitale Technologien revolutionieren gerade die Produktion und Organisationprozesse drumherum. Unternehmen, die ihre Effizienz steigern und wettbewerbsfähig bleiben möchten, stehen früher oder später vor der Herausforderung Digitales Shopfloor Management zu...
Verbesserung des Shopfloors und des Managements: Wie Digital Shopfloor Management Software Unternehmen transformiert
In der modernen Produktionslandschaft stehen Unternehmen vor der Herausforderung, unterschiedliche Unternehmensbereiche wie Shopfloor, Entwicklung und Geschäftsführung effektiv miteinander zu verbinden. Während auf dem Shopfloor Liefertermine und Stückzahlen im...